
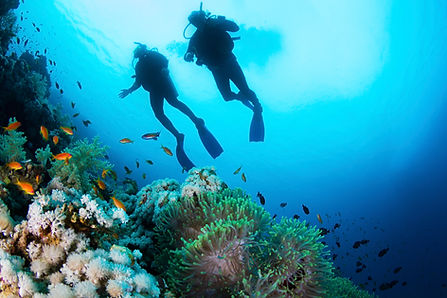
Coral Reef Restoration Project at University of Hawai'i at Mānoa
Destructive Testing
Destructive testing was used to validate the FoS and failure mechanisms predicted by FEA on a critical component. For this test, it was decided that with the funds and time allotted, a single destructive test would be sufficient for the proof of concept and for comparing SolidWorks simulations. The machine used for the compression test was a 300k-lb. Material Test System (MTS). The materials used in the test are one custom Inner and one Outer joint, one 7.15’ FRP beam, two 1.5’ FRP beams, and 16 0.5” x 7” zinc plated bolts, nuts and washers. The 7.15’ beam was connected to the two custom joints using 2 bolts on the outer joint end, and 4 bolts on the inner joint end. The horizontal beam was supported by the two 1.5’ beams, and attached to the bottom of the joints using four bolts on each end. Once the Inner-Outer joint connection was assembled, it was placed center to the loading platform of the MTS test frame and then stabilized using ratchet straps. A weight distributing I-beam was installed between the loading platform and the horizontal beam to distribute the load evenly to two points on the beam. The contact points of this beam were placed approximately 1’ from each end of the beam, and 5’ from each other. This beam sat on top of the FRP custom joint beam to produce a more uniform load. Gridded sheets with squares measuring 1 cm were set behind each joint to measure displacement.

Figure 1. Deflection and Pressure Results of Destructive Test on FRP Beam and Custom Joints
Based off of these results, the test shows that both the prefabricated FRP beam and the custom joints which have much thicker walls significantly surpass the predicted FoS. Failure of the assembly, happened at approximately 18,000 lbf and at the lower bolt holes as predicted by the FEA.